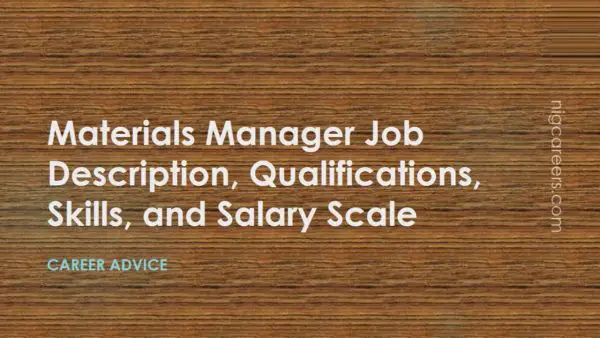
Materials Manager Job Description, Skills, and Salary
Get to know about the duties, responsibilities, qualifications, and skills requirements of a materials manager. Feel free to use our materials manager job description template to produce your own. We also provide you with information about the salary you can earn as a materials manager.
Who is a Materials Manager?
Materials management is a subset of business logistics and refers to the oversight of physical items or products’ location and movement. Spare parts, quality control, and inventory management are the three primary components of such management. Materials management is critical in large manufacturing and distribution environments, such as warehouses, where multiple components, locations, and significant financial investment are involved.
With increasing global demand for raw materials, businesses rely on materials managers to manage these resources. Typically, a company hires a materials manager to monitor and optimize the use of materials used to manufacture products for sale to general, commercial, and government customers. This is a critical role within a manufacturing or construction company that relies on careful material allocation during production.
A materials manager is frequently not only responsible for managing materials, but also for purchasing them. Since costs vary according to the scope and type of materials used, the materials manager must understand how and when to purchase the highest quality materials at the best price to maximize the company’s benefit. In general, a materials manager works closely with the executive management team to ensure that company objectives are met on current and future projects.
To effectively supervise this responsibility, the materials manager collaborates with logistics managers to routinely evaluate existing projects with the materials required to produce finished products. This requires continuous inventory monitoring via a supply chain management system. Occasionally, it is also necessary to maintain spare parts on hand for use in repairing returned products as part of a refurbishment program.
Another critical function of the materials manager is to coordinate efforts with the design or engineering teams. This is to ensure that when products leave the shop, they meet or exceed industry standards for quality and performance. Each project must be thoroughly examined and the necessary materials located and purchased to meet these requirements. Failure to manage this aspect of the process effectively can have serious ramifications for a business.
Materials managers typically have experience managing raw materials and inventory within their chosen industry. This position requires familiarity with the materials used to manufacture specific types of products. This can be gained through years of on-the-job experience or specialized training provided on-site.
Additionally, the materials manager’s job requires resourcefulness in locating raw materials necessary to produce the products that consumers require. This typically entails establishing a strong working relationship with vendors and suppliers of the components and materials required to complete the job. Additionally, it requires the ability to negotiate the best prices and delivery rates to ensure that projects are completed on time and within budget.
Materials management is critical for many businesses because it ensures the proper tracking of various goods within an organization. This can include products manufactured by a business as well as supplies and materials purchased from another manufacturer. Each of these items has a direct financial value for a business, and many companies hire individuals to oversee such materials.
Materials managers may deliver materials to supply bases, ensuring that they arrive on time and are of a high standard of quality. Additionally, they may coordinate consumer delivery processes, which may include budget management, freight acquisition, inventory monitoring, and inventory accuracy. Materials managers may also be involved in new product launches and customer charges, depending on the size of their organization.
Materials management objectives vary according to situational factors such as industry and organization size. The precise process of materials management will vary according to the unique requirements of an organization. Despite this, there are three primary materials management objectives that nearly all organizations attempt to achieve through their processes, including the following:
- Superior quality
Materials managers want to purchase high-quality goods and services. Assuring the quality of materials can aid in the efficient progression of manufacturing and product development processes. As a result, a materials manager may inspect the quality of goods from various suppliers before making a purchase. This enables them to maintain the high standards of quality demanded by consumers throughout all manufacturing processes.
- Sufficient amount
Materials managers strive to purchase goods and services in the appropriate quantity. Manufacturing companies must maintain the appropriate level of inventory. This can help mitigate the risk of having too much or too little inventory, reducing costs associated with excess inventory storage and the need to make last-minute purchases of sometimes more expensive materials to compensate for a lack of inventory.
- Consistent timing
Materials managers’ primary objective is to procure goods and services at the optimal time. They want to ensure that they can acquire materials consistently to maintain production processes without experiencing a supply shortage. As a result, material managers strive to maintain a steady supply and flow of the raw materials required to sustain operations. To accomplish this, materials managers must monitor inventory regularly and be familiar with shipping procedures.
Materials Manager Job Description
Below are the materials manager job description examples you can use to develop your resume or write a materials manager job description for your employee. Employers can also use it to sieve out job seekers when choosing candidates for interviews.
The duties and responsibilities of a materials manager include the following:
- Conducting due diligence on potential vendors and negotiating prices.
- Collaborating with management to determine supply requirements.
- Recommending improvements to the existing processes to decrease waste and increase output.
- Keeping track of and evaluating the quality, movement, and expenditure of all materials.
- Managing the organization’s supply distribution.
- Keeping an eye on inventory levels and material access.
- Assembling forecasting models in collaboration with management.
- Supervising and assisting subordinates and new hires.
- Maintaining detailed records of procurement activity, quantities purchased, and vendors.
- Collaborating with other supervisors to ascertain supply requirements.
- Acquiring supplies and materials following specifications
- Coordinating and supervising procedures for receiving and warehousing
- Supervising the organization’s supply distribution
- Developing and implementing a process for inventory cycle counting to ensure high inventory accuracy.
- Sustaining supervision, evaluation, and coaching of subordinates
- Maintaining relationships with suppliers and negotiating with them
- Maintaining detailed records of procurement activity, material quantities, and specifications, among other things.
- Ascertaining that computer systems are updated on a timely and accurate basis.
- Preparing inventory, material usage, and efficiency reports.
- Resolving shortages of labor and materials, backlogs, and other potential schedule disruptions
- Developing strategic solutions to enhance material flow on a variety of levels
- Conducting interviews with vendors and visiting supplier distribution centers and manufacturing facilities to ascertain and learn about pricing, products, and services.
- Attending conferences, trade shows, and meetings to build relationships with suppliers and gain knowledge of emerging industry trends
- Analyzing financial statements, price proposals, and other pertinent information to arrive at a reasonable price
- Contracting negotiations on behalf of the organization and agreement-making with suppliers regarding product delivery
- Meeting with vendors and employees to discuss unacceptable and defective products and to develop corrective action plans
- Conducting contract evaluations and monitoring to ensure suppliers and vendors adhere to contract terms and conditions
- Maintaining and reviewing inventories, product performance, deliveries, costs, and purchased items
Other important tasks include the following:
- Production planning
Material managers must devise the most efficient method of meeting consumer demand. They must establish priorities for material flow, including what materials are required for production and when they will be required — a process known as forecasting. After establishing priorities, materials managers will manage workflow to ensure that the appropriate capacity of materials is available to meet those priorities.
- Implementation and control
Materials managers are accountable for carrying out the production plans they develop. They may monitor and control production activity to meet the objectives outlined in their plans. Additionally, materials managers must execute purchasing plans to meet their objectives.
- Inventory control
Materials managers are responsible for inventory control. They must keep track of the inventory on hand at all times and safeguard their business against producing excess inventory or experiencing a shortage of inventory. Materials managers frequently purchase additional materials when inventory levels fall below a predetermined level to ensure a continuous flow of resources.
Materials managers frequently monitor specific operations related to material procurement. They typically have an understanding of how operations work and how to schedule production processes effectively to meet delivery targets while maintaining overall cost-effectiveness. Additionally, managing operations entails planning the numerous logistics that support distribution schedules.
It is critical for materials managers in larger companies to plan and control the facilities, plants, equipment, and labor that are available to process work and produce inventory. Knowing when they can expect work to be processed can assist them in maintaining a smooth flow of materials.
Qualifications
- A bachelor’s degree in logistics or a related field is required.
- A minimum of five years’ experience in a comparable position.
- Experience in management is a plus.
- Thorough knowledge of supply chain and inventory management systems.
- Expertise in forecasting and budgeting processes.
- Excellent communication and leadership abilities.
- With an analytical mind and superior problem-solving abilities.
Essential Skills
- Strategic Sourcing and Purchasing
Strategic sourcing and purchasing is the deliberate process of selecting the appropriate materials in the appropriate quantity, at the appropriate time, for the appropriate purpose. This process includes procurement decisions, which involve the selection of vendors and materials.
Materials planning preparation
Material planning preparation is the process of scheduling, planning, and inventory control that determines the manufacturing processes in terms of material requirements and output.
- Capacity planning
Capacity planning is the process by which an organization determines the number of products required to meet the demands of its customers. The design capacity, on the other hand, is the volume of product demand that the organization can meet.
- Process planning
Process planning is the use of technology to aid in the manufacturing of products and in the organization’s arrangements to meet its requirements.
Forecasting and Demand Management
Demand management is the process of forecasting the demand that an organization may have to meet. Forecasting is a technique used to forecast the actual demand that an organization will experience throughout a manufacturing cycle.
- Sales and operations planning
Sales and operations planning is the process of synchronizing all manufacturing processes to manage the supply chain effectively.
- Risk Assessment
Risk management is the strategic management of manufacturing processes through the control of static and dynamic materials, to ensure that an organization can maintain profitability rather than engage in activities that increase production costs and inventory holding.
How to Become a Materials Manager
To work as a materials manager, you may need a combination of post-secondary education, training, and experience in supply chain management. By networking with materials management professionals, you can learn about job openings. Experiential knowledge of a particular material management system may also provide an advantage. Residents of areas with little manufacturing may choose to relocate in search of work.
Numerous employers prefer that material managers hold undergraduate degrees in business or supply chain management. Employers with larger workforces, particularly those with intricate supply chains, may prefer candidates with advanced degrees. Certain raw materials, such as chemicals, require someone with scientific expertise to manage effectively, and companies that use these materials may hire candidates with a related scientific degree. If you’re interested in becoming a materials manager, consider the type and plan your education accordingly.
Certification in material management may also assist you in advancing your career as a materials manager. The certification can attest to your knowledge of materials management techniques and your dedication to this field. Conduct research on these programs to ensure the one you’re considering is highly regarded in your field.
Along with education, experience in this field may be required to become a materials manager. Pursue an internship or a part-time job while in college, perhaps as an inventory control clerk or a similar position. Employers may decide to hire you on a full-time basis following your graduation. If you have a bachelor’s degree but lack experience, you can begin your career in purchasing or inventory monitoring and work your way up to materials management.
Networking can assist you in advancing your career as a materials manager. Numerous disciplines, such as purchasing and inventory control, have local chapters of trade organizations. Participating in a local chapter, particularly in leadership positions, can help you develop relationships with people who can alert you to job openings. Your chapter’s leadership skills will help you become a more desirable candidate. Additionally, online forums can help you network and learn about job opportunities.
Certain businesses prefer to hire materials managers who are familiar with the company’s materials management computer system. If possible, you should seek employment with a company that uses a standardized system to increase your chances of becoming a materials manager elsewhere. The hiring company may value your familiarity with its system.
This is a prevalent role in manufacturing firms. If you live in an area with little manufacturing, even with education and experience, becoming a materials manager may be difficult. Relocating to a region with a strong manufacturing base will make finding work easier.
Where to Work as a Materials Manager
Materials managers work in a variety of settings, but the majority of their time is spent in warehouses.
Materials Manager Salary Scale
In the United States, the national average salary for a Materials Manager is $83,213 per year.
Manufacturing and Production, Transportation Distribution and Logistics