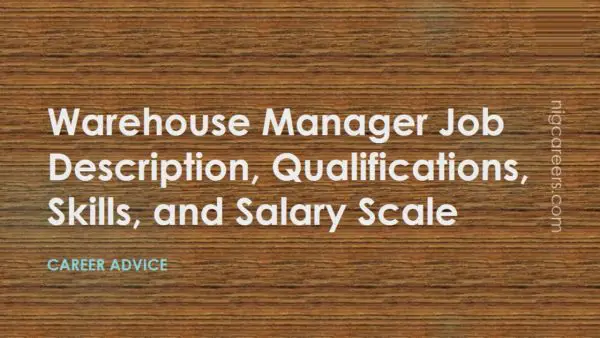
Warehouse Manager Job Description, Skills, and Salary
Get to know about the duties, responsibilities, qualifications, and skills requirements of a warehouse manager. Feel free to use our warehouse manager job description template to produce your own. We also provide you with information about the salary you can earn as a warehouse manager.
Who is a Warehouse Manager?
Warehouse managers are supervisors at product storage facilities or distribution centers. They are responsible for supervising workers and creating new policies to increase productivity, safety, quality, and efficiency. Administrative duties include scheduling, hiring, and training employees.
Warehouses can be busy and can be large places to work. All freight that arrives on trucks from manufacturing plants has to be unloaded, checked, and stored following the industry policy and guidelines. Orders for outgoing goods are collected, packed, and returned to trucks for distribution. The warehouse manager is responsible for ensuring that shipping procedures to and from the destination and returning products are as efficient and accurate as possible. Managers delegate tasks to workers and direct them to ensure that things run smoothly.
A warehouse manager’s main job is to manage human resources. Managers identify the need for additional labor and advertise openings. They also hire new employees. A manager might offer training courses to groups of workers or personal on-the-job training for employees. To help workers improve their productivity, managers often conduct regular performance reviews. To resolve a problem, workers can talk to their warehouse manager if they have a concern.
Warehouse managers conduct walk-throughs in their workplaces to ensure that workers comply with safety regulations and that equipment and facilities are maintained. To identify and correct potentially dangerous situations, managers must be well-versed in both federal and regional occupational safety codes. Managers should research and buy new equipment when needed to increase productivity and safety.
Although the requirements for becoming a warehouse manager are different from employer to employer, most managers get their jobs after several years of working in entry-level warehouse jobs. Warehouse owners prefer to hire existing employees rather than hiring new managers, as they are more familiar with their company’s daily operations, policies, and expectations. To be able to work in a large facility, a bachelor’s degree or more in business administration, human resource management, or occupational health is necessary. If warehouse manager excels in their job, they may be able to move up the ranks to become an executive.
Customers can use warehouses or storage facilities to store all kinds of goods for a set time. Some special arrangements and facilities are required depending on the item being stored. The warehouse manager is responsible for ensuring that the warehouse has the equipment and space necessary to store the items its customers need. They must also maintain an inventory of all items and follow a strict organization plan to ensure that items can be quickly retrieved if needed.
Warehouse managers are most commonly employed in storage businesses. These businesses offer a variety of storage services. They may be able to work with larger companies or businesses that have enough storage space to require someone to manage them.
Warehouse Manager Job Description
Below are the warehouse manager job description examples you can use to develop your resume or write a warehouse manager job description for your employee. Employers can also use it to sieve out job seekers when choosing candidates for interviews.
The duties and responsibilities of a warehouse manager include the following:
- Describing storage policies and spaces available to customers
- Assuring that there is enough storage space for both customers and employers.
- Offering special arrangements to customers with special needs for goods
- Informing customers about storage fees based on volume, weight, or time, according to company policies.
- Customers and employers receive regular reports on the products in their stores.
- Reviewing and adapting warehouse operations following shipping schedules.
- Inspecting warehouse conditions and vehicles, tools, or equipment.
- Assisting in the sorting, labeling, and storage of all received products, items, or materials according to company policies.
- Issuing lists of all incoming items and delivering them to the receiving personnel.
- Preparing a list for outgoing shipments based on customers’ requests.
- Assigning work schedules and timesheets.
- Assisting warehouse workers in their daily tasks, when needed
- Assisting in receiving, warehousing and distribution by initiating, coordinating, and enforcing programs.
- Controlling inventory levels by performing physical counts and reconciling with data storage systems.
- Planning and implementing new layouts to maintain the warehouse’s physical condition.
- Achieving financial goals by creating an annual budget, scheduling expenses, and analyzing variances.
- Completing warehouse operations by scheduling and assigning employees
- Enhancing employee performance through coaching, counseling, or disciplining.
Other important tasks include:
Sending and receiving shipments
This will include overseeing the loading and unloading of shipments. You may also be responsible for daily warehouse operations and creating shipment schedules.
- Tracking inventory levels
Software programs will be used to track inventory levels. You might start shipments to other facilities if inventory levels are too low or high.
- Examining safety and security procedures
You will be responsible for ensuring safety and security in the facility. Most warehouse managers adhere to the Occupational Safety and Health Administration’s (OSHA) standards.
- Examining equipment and goods
You inspect the shipments to ensure that they are in good condition. To ensure they are in good shape, you may also inspect equipment and tools.
- Building and managing teams
This managerial role is responsible for managing staff and teams. This role may include managing staff, assigning schedules, and overseeing employee training.
- Communicating with clients
Many warehouse managers communicate with their clients via email and phone. To schedule shipments or coordinate equipment requirements, you might communicate with suppliers and vendors by phone or email.
- Oversee the maintenance of machinery, vehicles, and equipment
Assist in the operation and maintenance of automated storage and retrieval systems as well as warehouse management systems.
- Visit customers to assess the service quality.
Maintain safety standards, hygiene, and security in the workplace. This includes ensuring stock like chemicals and food is stored safely.
Qualifications
These skills and education experience are required for many warehouse manager jobs:
Education
General Education Development (GED) or a high school diploma is required for warehouse managers. This gives you a solid foundation in math, language, and reasoning.
Training
Warehouse managers receive essential training in entry-level positions. These roles will give you the experience you need:
- Material mover
These professionals work in warehouses and are responsible for moving freight and goods. You might use forklifts or pallet jacks to move goods and may also accept deliveries from trucks. You might be a material mover and help with the packing, loading, and maintenance of warehouse layouts.
- Warehouse clerk
These specialists are essential to the management of supply chains. These specialists often work in warehouses where they help schedule deliveries, track inventory, and monitor products. You might be required to inspect and handle defective products, create inventory charts, or analyze supply chain data.
Certification
Warehouse managers often need to be certified to operate heavy equipment such as forklifts or aerial lifts. These credentials can be obtained from many vendors. Most require both a written and practical exam. These certification programs are offered by many employers.
Essential Skills
- Organizational Capability
Great warehouse managers are more than just skilled in administrative organization. They also know how to use all tools available to them to ensure that operations run smoothly. They have an excellent sense of how to manage people and processes to ensure high levels of organization and productivity. Check out these 5 Warehouse Organization Tips.
- Precision
Warehouse managers are required to be precise in their warehouse management. This means being able to keep track of all details, using technology when possible, and effectively using it. Failure to manage the inventory and warehouse side of a business can lead to major problems.
- Tech-Savviness
Technology is now the best friend for any warehouse manager. A warehouse management system should be the foundation of every warehouse manager’s business. Many upgrades can be made to improve operations efficiency. For example, employees can use handheld barcode scanners.
- Safety-Mindedness
Warehouse safety must be a priority. An effective warehouse manager will always keep this in mind. It is important to prevent injuries from becoming too frequent. This will result in happier employees, better productivity, and overall operational improvement.
- Leadership
A warehouse manager must have people skills. This includes the ability to motivate and lead employees. Great warehouse managers set a good example by showing respect for their coworkers, listening and welcoming others’ ideas, being fair and understanding with their subordinates. Leaders have a core competency that allows for them to delegate but also understand the tasks being given to them.
- Integrity
Untrustworthy warehouse managers are not what a business needs when they have a lot of inventory worth thousands of dollars. A warehouse manager who is trustworthy, honest, and ethical is needed. Although theft and inventory shrinkage are common problems in business, you want to know that your manager won’t be the cause.
- In-depth knowledge of different warehouse management software
High-tech rules are the norm when it comes to building an organization’s digital infrastructure, as with many other current trends. Warehouse management software systems (also known as WMSs) are essential for modern warehouse managers. They provide the organizational models that keep modern operations up and running. Managers should understand how WMSs and other more complex systems like WESs work to make them as efficient as possible.
- Ability to invest and research in automation
Today’s e-commerce giants offer lightning-fast fulfillment to their customers, making it difficult for competitors. This automation is easy to implement and very affordable. An automation integration and purchasing manager should be able to keep their fingers on the pulse of new and established technologies.
- Understanding the importance of warehouse layout
The design of a warehouse layout is an essential building block for operational success. Even though a warehouse manager may be well-versed in this art, that doesn’t necessarily mean they can see the big picture into the future. The process of creating a warehouse layout doesn’t end when the physical infrastructure has been put in place. Instead, it must be flexible enough that it can be reconfigured during peak times or other disruptive events. Warehouse managers can provide the necessary skills for all departments to test and create in the most efficient manner possible once they have been trained.
- Ability to emphasize associate training
Companies must look for alternative ways to fill their shifts as product demand increases. The company “Wonolo” makes it easy to find top-notch operational support when you need it most. Even the most skilled warehouse associates need to be provided with accurate and thorough leads. The warehouse manager is responsible for ensuring that all warehouse associates have the correct information. These associates often have a lot of experience but can’t work at their best if they aren’t given specific goals and processes.
How to Become a Warehouse Manager
- Get a high school diploma.
Before applying for a role as a warehouse manager, you should complete your high school education. Employers will accept either a diploma or a GED. This credential will confirm your knowledge of science, math, writing, and verbal communication. You can also learn soft skills such as organization and problem solving by completing your high school education.
- Get work experience.
You will need to have worked in warehouses for at least two years before you can become a warehouse manager. You can start as a material mover, or material recording clerk, and then go on to work in a supervisory role for another year.
- Cultivate essential skills.
You can gain valuable experience in supply chain management and shipping logistics by pursuing opportunities that will allow you to sharpen your skills as a warehouse manager. You can sign up for training sessions to enhance your customer service or teamwork skills. To improve your leadership skills, you may ask for additional responsibilities or request that you manage a project.
- Management training complete.
You can position yourself as the best candidate for this role by completing a management program or gaining experience managing people and tasks. You can register for a training class at work or at your local community center. You can become a team supervisor to gain first-hand experience. This allows you to manage and lead projects.
Where to Work
Warehouse managers manage a variety of goods, including supplies and materials as well as products for retail. Warehouse managers are usually full-time workers and may work irregular hours. They can adjust their schedules to send or receive shipments as needed. They typically work in warehouse offices.
Warehouse Manager Salary Scale
Warehouse managers work full-time. Their salaries are based on their work experience, company industry, and geographic location.
The average salary in the U.S. is $57,645 annually.